Article of the Month - September 2022
|
Proposed 4.0 Industrial Management System for
daily operations that poses point cloud assets with annotated real-time
sensory measurements and utilizes unsupervised alert logic
Ion Anastasios KAROLOS, Stylianos BITHARIS,
Vasileios TSIOUKAS, Christos PIKRIDAS, Sotirios KONTOGIANNIS, Theodosios
GKAMAS, Nikolaos ZINAS, Greece
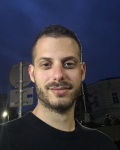 |
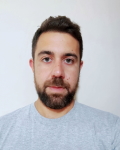 |
 |
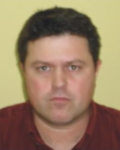 |
Ion Anastasios
Karolos |
Stylianos Bitharis |
Vasileios Tsioukas |
Christos Pikridas |
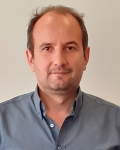 |
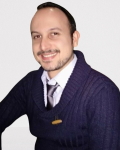 |
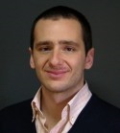 |
Sotirios
Kontogiannis |
Theodosios Gkamas |
Nikolaos Zinas |
This article in .pdf-format
(24 pages)
SUMMARY
The safety and enforcement of preventive maintenance procedures
specifically for equipment in large industrial infrastructures is a
matter of major importance in the Oil and Gas industry. Historically,
industrial maintenance operations were executed only when strictly
necessary. However, in industrial manufacturing environments,
maintenance processes are stochastic, dynamic, and complex. Nowadays,
the maintenance paradigm is changing, and industrial maintenance is now
understood as a strategic factor and a profit contributor to ensuring
productivity in industrial systems. An important parameter to satisfy
this point is the production of digital twins, which can be derived
through an accurate and detailed survey. This paper presents a holistic
industry 4.0 solution towards industrial maintenance. The study focuses
on the oil refinery industry and presents their proposed maintenance
system architecture, system implementation, technical and basic
functional characteristics. The current study took place at Hellenic
Petroleum facilities in Northern Greece.
1. INTRODUCTION
Daily management, or daily huddle, has been successfully used by many
companies such as the oil and gas industry for their planning and
follow-up of the daily operations. In addition, the methodology is often
used in parts of the organization, company, or Industry. By visualizing
work-hour plans of specific machines and having daily short meetings, a
maintenance plan can be created and assigned, solving problems directly
and steering the operations to be performed.
Traditional Industrial processes focus only on automation and
isolated per machinery data collection. SCADA/DCS systems were the first
critical step for process automation. In addition, the 4.0 roadmap
enforces the use of centralized cloud storage of Industrial information
and cloud computing processes, including data mining and machine
learning algorithms. These processes will include all Industrial assets
assisted by cloud-connected sensors and IIoT as well as Cyber-Physical
Systems and 3D representations of physical objects called assets
(Lampropoulos et. al., 2019).
Industrial IoT and machine learning focused on failure detection in
production lines can be achieved by utilizing IoT concentrators for
issuing real-time alerts and propagating sensory measurements, and using
MQTT brokers over Industrial wireless communication technologies
(Silvestri et. al., 2020), such as NBIoT, LTE, Industrial Wi-Fi, and
LoRa (Nurelmadina et. al., 2021). Furthermore, the IoT integration can
offer important features that can be exploited by machine learning
algorithms included in orchestration frameworks similar to the one
proposed by (Carvajal et. al., 2019).
Following this trend, Augmented Reality processes have also been
proposed to be incorporated as parts of the industrial maintenance and
training processes using mobile phone applications (De Pace et. al,
2018) and the utilization of optical see-through devices (Pierdicca
et.al., 2017). Such initiatives trigger the necessity of virtual
objects, the encapsulation of such objects with sensory measurements, as
well as the interoperability of such objects with management operations
directly provided from the field.
The increasing use of the Internet of Things (IoT) in factories, and the
AR advancements, where assets are connected to the Internet and extend
their use via the development of features, eventually leads to the use
of Virtual Reality (VR) for Industrial processes and machinery
maintenance training. Virtual Reality headsets provide an additional
capability for basic training recruits and Industrial problems
visualization and simulation (Liagkou et.al., 2019).
Nevertheless, significant challenges are still lying ahead, such as
security and privacy, data heterogeneity, management of smart processes
for optimal decisions, and standardization (Sanchez et. al, 2020).
This paper uses as digital objects terrestrial 3D laser scanner surveys
which took place at the Hellenic Petroleum facilities in Northern
Greece. Digitizing the complex installations, with the use of IoT and
cloud facility management processes, the Industry can increase the
performance of the daily industrial management by adding digital
features in 3D objects, like real-time indicators, pressure,
temperature, and vibrations of a pump or compressor. Furthermore, the
authors' proposed framework and system architecture, including the
processes for Industrial maintenance, focusing on Oil industry
infrastructures and assets, is presented.
2. RELATED WORK ON POINT CLOUD - GIS
SERVICES AS PARTS OF INDUSTRIAL SYSTEMS FOR PERSONNEL OR ASSETS
Usually, all studies so far have kept "close" proprietary files and
have been done using desktop tools easily leveraged to deceive an
unsuspecting public. Therefore, the authors used a web tool for viewing
the 3D survey in this study. Web service is a quick and easy way to
share your point cloud data with anyone, regardless of their familiarity
with 3D models. In addition, some of its features include distance &
area measurements, height profiles, clip volumes, various point
rendering qualities (square, circle, interpolation, splats), and
different types of materials or characteristics. For that reason, the
Potree Webtool (TU Wien, 2016, Schuetz, 2016, Carey et al., 2021) has
been chosen. Potree is a free and open-source webGL based viewer for
large point clouds, e.g., 20 billion and more. It is based on the TU
Wien Scanopy project and several other research projects. Some of its
features include distance & area measurements, height profiles, clip
volumes, various point rendering qualities (square, circle,
interpolation, splats), and different materials. The figure illustrates
a screenshot from the Potree environment of a Continuous Catalytic
Reforming (CCR) unit with the basic associated tools.
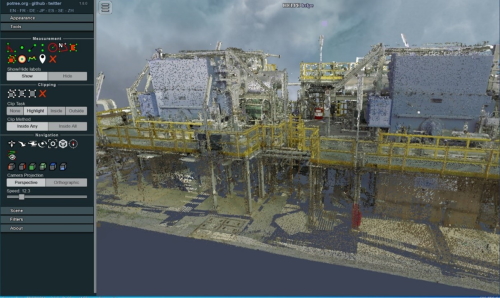 |
Figure 1. 3D point cloud view of a CCR unit using
Potree environment
3. INDUSTRIAL MAINTENANCE SYSTEM HIGH-LEVEL ARCHITECTURE
Industrial maintenance has evolved significantly towards digital
transformation over the last few years. Historically, industrial
maintenance operations were executed only when strictly necessary.
However, in industrial manufacturing environments, maintenance processes
are stochastic, dynamic, and chaotic. Industrial Maintenance processes
are crucial issues that ensure production efficiency since unexpected
disturbances lead to the loss of productivity. Therefore, maintenance
acts mainly as reactive and preventive to avoid production disruption,
being the predictive strategy only applied for critical situations.
Traditionally, maintenance strategies do not consider the huge amount
of data generated and the available emergent Information and
Communications Technology (ICT), e.g., Internet of Things (IoT), Big
data, advanced data analytics, cloud computing, and augmented reality.
However, the maintenance paradigm is changing, and industrial
maintenance is now understood as a strategic factor and a profit
contributor to ensuring productivity in industrial systems (Faccio et
al., 2014). Furthermore, Industry scaled sensory data generation
requires a different schemaless storage approach, different from the
existing relational database solutions used by Industrial Management
systems (Asiminidis et al., 2018).
In this paper, the authors provide a holistic solution industry 4.0
solution towards industrial maintenance. The authors focus on the Οil
refinery industry maintenance and present their proposed management
system architecture, system implementation, technical and functional
characteristics in the following sections. Figure 1 illustrates the
authors' proposed high-level system architecture.
Towards the direction of Industrial Maintenance and Industry 4.0, the
authors propose a framework consisting of the following actions as part
of their approach and methodology that ensembles their proposed system
architecture:
Action 1: 3D Industrial models and 3D Industrial
infrastructures representation. The 3D industrial assets and
infrastructures representation over the cloud is a significant step for
visualizing and monitoring personnel and assets. It leads to the
enforcement of digital twins via implementing the Resources Management
system and its accommodated services for data management and monitoring
purposes. Additionally, the definition of access zones and the
utilization of GPS/Indoor position technologies such as BLE and UWB will
provide additional location-based services for both personnel and
Industrial assets.
Action 2: Centralized and normalized maintenance processes.
This action includes developing cloud services provided by a Resources
Management system. This system includes processes and plans per
machinery (asset), historical maintenance information, technical
specifications, and guidelines for maintenance operations. It also
interfaces with already stored Industrial parts per asset,
personnel/assets tracking services, generate tasks, and issue alerts and
notifications. In addition, the proposed system will be capable of
interacting with mobile tablets and exchanging real-time information
with the maintenance personnel in the field.
Action 3: Centralized assets sensory repository and machine
learning processes. The proposed Resources Management System
includes appropriate sensory storage engines, where all sensory
information per asset is stored in real-time. Appropriate Industrial
Wi-Fi/NBIoT/LoRa infrastructure, utilized to collect machinery
data. The collected data are sent to the cloud logging service.
Additionally, deep learning and data mining processes are utilized for
monitoring and management purposes. Appropriate sensory data
visualization is offered to the mobile end node devices (tablets) using
secure transmission channels as part of asynchronous management or
requested industrial maintenance tasks.
Action 4: Unified system including AR capabilities and VR
training methods. Includes integrating the assets as objects
rendered by mobile devices (tablets) and their provided AR capabilities
to implement services such as 3D draw and send or 3D alerts illustration
and 3D illustrative maintenance using 3D rendering and 3D annotation.
Additionally, the use of pre-trained convolutional neural networks and
image segmentation techniques will also be used as part of the assets or
assets malfunction placement detection. Finally, VR technology is
included as part of personnel facility guidance and training for
specific Industrial maintenance operations.
Based on their framework proposition and methodology, the authors
propose a new system for technical maintenance for the oil refinery
industry. The main industrial parts applied to the proposition are
flammable gas or liquid pumps and compressors. The proposed system is
presented in Figure 2 and includes the following components:
Figure 2. Proposed Maintenance system for Oil
refinery industries high-level architecture
Data Collection component: Data collection component
includes the cloud database engine for the MMS, the 3D point cloud data
storage for the point cloud factory and assets visualization, and the
NoSQL database for the collection of assets sensor measurements, divided
per asset I.D. The data collection component also includes the agents
and services for collecting, securing the data (data acquisition and
logging services), and providing the data. Data acquisition for the MMS
component for tasks and processes is performed over SSL HTTP POSTS
(Kontogiannis and Asiminidis, 2021). Data acquisition for the personnel
positioning service is performed using NodeJS HTTP over AES-128
encrypted data streams (Yassein et al., 2017, Profanter et al., 2019).
Data acquisition for sensory data is performed via TLS-MQTT AES-128 and
base64 encoded data streams. Finally, 3D A.R. annotated point cloud
information is acquired using SSL DAV/ secure FTP services.
Maintenance Management System component: The MMS
component is a cloud-based system that includes its relational Database
such as PostgreSQL, SQL Server, or Oracle SQL. The Management system
includes the logic and display functionality for periodic maintenance
tasks and the steps to be followed per asset. The MMS component can
provide via the Web: 1) pumps and compressors (called assets)
categorization and assets description manager, 2) a historical assets
maintenance information dashboard, 3) tasks and processes manager for
the creation of tasks, 4) maintenance personnel manager for the process
of tasks assignment, 5) automated digital forms creation for repair
procedures and static digital forms for maintenance procedures, 6)
procedures recording and forms logging functionality. Additionally, the
MMS component should include a mobile tablet app for the issue of
notifications/tasks and procedures reporting to the field engineers.
Communication between the cloud Web platform and the mobile tablet app
will be over secure 5G/6G cellular installations channels or the
factory-protected Wi-Fi installation.
Factory AR visualization component: This component
includes the appropriate point cloud 3D representation of the factory
establishment with geofenced zones and on-demand assets 3D rendering at
the mobile device end. The factory representation includes a Web-based
3D point cloud view of the factory, with geofenced and georeferenced
ATEX zones (ATEX-137, 1992) and real-time marks of the personnel
position in the point-cloud render. The positioning of the personnel is
performed with the use of a positioning service installed at the
personnel's mobile devices. This service transmits GPS positioning
information for open area installations or BLE/UWB proximity information
for indoor establishments (Karaagac et al., 2017, Schmidt et al., 2018).
The factory A.R. component also includes the functionality of alerts
generation for restricted zone access and the addition of sensory and
informative augmented annotations to either the Stats Manager of the
sensory component or the Tasks Manager of the MMS component. The
Web-based 3D point cloud render of the compressor or pump also includes
asset annotations, where maintenance process steps information is
presented at the mobile device. Asset authentication is also available
using Q.R. code scanning or asset image detection from the mobile
device's camera.
Sensors component: Proposed maintenance systems
sensors measurements stored by the Data collection component must be
accessible to other processes, algorithms, and interfaces with other
systems. In this case, data input comes from existing pump and
compressor sensors, focusing on the authors' implementation for Oil
refinery maintenance. Those sensors are mainly temperature, pressure,
and vibration sensors. Using Profibus or Industrial Ethernet, these
sensors measurements are concentrated at the Distributed Control System
(DCS) operator station HMI from the assets (pumps or compressors) field
control stations. Then from the operation station, the data are uploaded
to a cloud-based MongoDB Database (Harrison and Harrison, 2021). This
database acts as a centralized storage point offering statistical links
for plotting and 3D annotating sensor measures to the point cloud Web
component. The data collection component also includes agents and bots
capable of issuing assets notifications regarding assets status and
maintenance estimations. Such information is inferred using trained
regressors, machine learning classifiers, or Recurrent Neural Networks
(Tedjopurnomo et al., 2020, Bochie et al., 2021).
Mobile application component: The mobile application
includes the services and activities for more timely and less
error-prone asset maintenance tasks. It includes the Q.R. or asset A.R.
asset detection, instance segmentation (Hayder et al., 2017, Zheng et
al., 2021), or A.R. asset segmentation via point cloud group
similarities (Wang et al., 2018). The MMS positioning service for indoor
and outdoor installations. The MMS maintenance tasks alerts and
notifications service and the A.R. visualization service provides
real-time sensor data, statistical data, and maintenance process steps
via assets annotation links (URLs) on top of point cloud layers. The
following section gives detailed information regarding the proposed
system components and functionality.
4. PROPOSED
MAINTENANCE SYSTEM INTERFACES AND SERVICES FUNCTIONALITY
The detailed description of the proposed Industrial Maintenance
system components is provided in the following subsections. At first,
the MMS component, services, and functionality are outlined. Then the
A.R. point-cloud visualization component is presented and its mobile
phone interface. Finally, the sensors management component is presented,
and the interoperability of the Q.R. asset detection with the
presentation of real-time sensor asset measurements via point cloud
annotations.
4.1 Maintenance Management System component
The purpose of the Industrial maintenance management system is to
store information regarding assets and incorporate the digital twins of
physical industrial assets to streamline the staff's predictive
maintenance and daily operations. First, basic information such as name,
type, serial number, manufacturer, and dimensions are recorded for each
machinery (asset). The Industrial Maintenance system also has the
capability of dynamic properties to cater to different asset categories'
different needs. Then the schedule maintenance plan is created by
uploading the relevant work orders and associated form templates for
every inspection. When a scheduled maintenance work order needs to be
performed, the assigned staff receives a notification regarding the
forthcoming activity. An important part of the industrial maintenance
system is its fault prediction of equipment parts ability, based on
time-series sensory data analysis and visualization for specific
metrics.
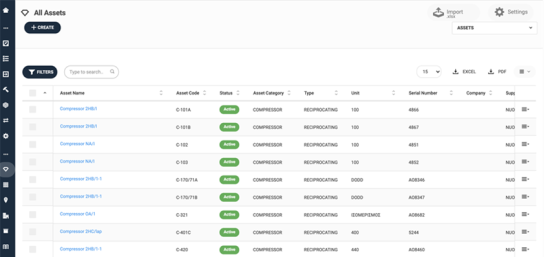 |
Figure 3. Recorded compressor assets in an
Industrial maintenance system
4.2 VR/AR visualization component and assets point cloud
representation
In this study, the 3D point cloud of each survey has been extracted
to a specific e57 format file, a compatible format for FARO SCENE lite
viewer. Then, each derived point cloud was then transformed into a
compatible virtual reality scene (see Figure 4), using the previously
mentioned software package. Finally, the user can interact with each 3D
object using the oculus Rift controllers and collect valuable asset
information.
Figure 4. Virtual reality with Oculus Rift S during
the survey of a compressor
The following figure (fig.5) illustrates the augmented reality
smartphone application based on the marker (Q.R. code method) for object
recognition and tracking. This smartphone app allows each user to
monitor critical indicators during complex machinery operations
(compressors or pumps).
Figure 5. Android-based smartphone app using marker
AR tracking
4.3 Sensors Measurements Component
The sensors measurements component is the core component for data
analysis and alerts prediction based on sensory input. It includes four
major parts: 1) The sensory database interface that connects the sensors
Measurements component to the data collection via appropriate JSON API,
2) The real-time and historical data representation called Stats
Manager, based on Telegraf and Grafana (Kychkin et al., 2019), 3) and
the raw data navigation and update called CRUD Manager for NoSQL data
(Jawarneh et al., 2018) and 3) Intelligent Agent (IAgent), that
traverses data via the JSON API providing assets predictions based on
past sensory data. The Stats Manager can provide detailed sensory
information per asset or sensor over time for interfacing with other
systems and services. The CRUD Manager is equipped with a JSON API for
remote requests over HTTP PUT or POST. Figure 6 illustrates the output
of the Stats and CRUD manager for a specific compressor asset. Figure
6(1) shows the real-time sensory data representations via the CRUD
Manager. In contrast, Figure 6(2) illustrates the compressor temperature
measurements graph and compressor vibration X, Y, Z-axis graph
measurements over time.
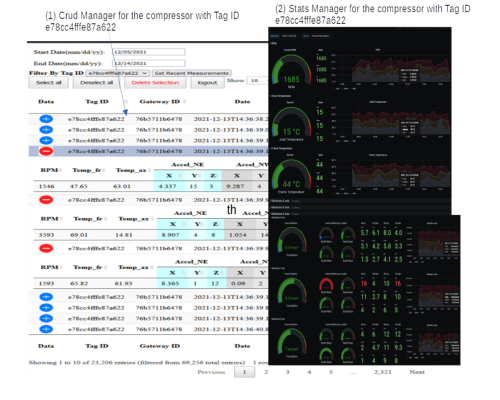 |
Figure 6. Compressor sensory component Stats Manager
and CRUD Manager output
An important piece in this intelligent and predictive maintenance
architecture is the decision support system for maintenance technicians
during maintenance interventions. This smart decision support system,
called IAgent, articulated with human-machine interaction technologies,
e.g. augmented reality, contributes to a faster and more efficient
reaction and recovery of the failure occurs when compared to paper
procedures. Its core functionality is the deprivation of critical assets
malfunctions by providing prior information using a per asset sensory
equipped part predictions of probable malfunctions.
In order to achieve that, a set of past data is required per sensory
asset part and alerts output issued for that part from the MMS
component. The volume of data needed depends on the max frequency of the
alerts monitored. For example, for sensory data stored per minute, ten
monitor alert types, and a max frequency of once a week, at least
100,000 sensory data points are needed for classifier train in a
supervised mode to provide accurate mapping to discrete alerts
(Windeatt, 2008, Alsariera et al., 2020, Saha et al., 2021). For alerts
issued for more complicated source inputs, meaning different asset
sensory parts or sensory types are contributing to the issue of the
alert, LSTM - RNNs are used to derive temporal patterns of prediction
(Wang et al., 2020). The further enhancements and evaluation of these
LSTMs using targeted compressors and their issued alerts are the
authors' ongoing research.
4.4 Mobile Application component
Augmented Reality (A.R.) can reduce maintenance process time and
improve quality by giving virtual information and assistance during
maintenance tasks. A set of experiments has been performed at (Havard et
al., 2016), showing -3% less maintenance time using tablets and -13%
using A.R. glasses from the standard process of paper-based maintenance
process performed with 25% fewer errors. Focusing on oil refinery
maintenance, the use of mobile phones or tablets requires special mobile
devices of appropriate safety regulations for zones of hazardous
materials called ATEX zone classes, divisions, and zones (ATEX-137,
1992). The maintenance compressors placed in an oil refinery
establishment follow Class 1/Division 2 Zone 2 ATEX directives for
mobile phones (ATEX-114, 2014) that signify ignitable concentrations of
flammable gasses, vapors, or liquids are in closed containers. Still, it
is likely to be released for short periods under normal operating
conditions.
5. CONCLUSIONS
This study presents a holistic Industry 4.0 solution towards
industrial maintenance. It focuses on the oil refinery industry where
complex machines installation exists. An important parameter that needs
to be satisfied by the proposed framework is the production of digital
twins, which can be derived through accurate and detailed survey
campaigns. A digital twin is a virtual representation of a physical
object or process. Implementing a VR-capable Industrial maintenance
framework is essential because it allows analysis of the data and
systems involved in a new concept before they can even happen. It is a
bridge between the physical and digital worlds. The proposed by the
authors' framework and system architecture under implementation is a
step towards this direction of primarily unifying and automating the
reporting maintenance processes and assets monitoring under a cloud
platform that incorporates 3D assets visualization. Being at the
forefront of technology, the Oil and gas industry already utilizes
dynamic software models and can take advantage of this proposed concept
to ensure efficient and safe ongoing operations and design new
techniques and facilities. For example, replicating physical equipment
or processes in a virtual environment can optimize asset and process
improvements in the virtual world before applying them in the real one.
This could be done by adding digital features like real-time indicators
like a compressor's pressure, temperature, vibrations, as well as other
maintenance actions that can trigger alert scenarios.
ACKNOWLEDGEMENTS
This research has been co-financed by the European Union and Greek
national funds through the Operational Program Competitiveness,
Entrepreneurship and Innovation, under the call RESEARCH – CREATE –
INNOVATE (project code: T2EDK-00708). Mr N. Maroulas, Mr. G.Giougkis and
Mr. D.Chrisikopoulos managing and technical staff of Hellenic Petroleum
refinery are highly appreciated.
REFERENCES
- Alsariera, Y. A., Adeyemo, V. E., Balogun, A. O., and Alazzawi,
A. K. (2020). Ai meta-learners and extra-trees algorithm for the
detection of phishing websites. IEEE Access, 8:142532–142542.
Asiminidis, C., Kokkonis, G., and Kontogiannis, S. (2018). Database
systems performance evaluation for iot applications. SSRN Electronic
Journal, 10.
- ATEX-114 (2014). ATEX 95/114: the ATEX Equipment Directive.
https://eur-lex.europa.eu/legal-content/EN/TXT/PDF/?uri=CELEX:32014L0034&from=NL.
Accessed at: 1/2/2018.
- ATEX-137 (1992). ATEX 137: the ATEX Workplace Directive.
http://eur-lex.europa.eu/LexUriServ/LexUriServ.do?uri=OJ:L:2000:023:0057:0064:en:PDF.
Accessed at: 1/2/2018.
- Bochie, K., Gilbert, M. S., Gantert, L., Barbosa, M. S.,
Medeiros, D. S., and Campista, M. E. M. (2021). A survey on deep
learning for challenged networks: Applications and trends. Journal
of Network and Computer Applications, 194:103213.
- Carey, C., Romero, J., and Laefer, D. (2021). New potree shader
capabilities for 3d visualization of behaviors near covid-19 rich
healthcare facilities. International Archives of the Photogrammetry,
Remote Sensing and Spatial Information Sciences - ISPRS Archives,
46(4/W4-2021):61–66.
- Carvajal, S. J., Tavakolizadeh, F., and Gyulai, D.
(2019). An online machine learning framework for early detection of
product failures in an Industry 4.0 context. International Journal
of Computer Integrated Manufacturing, 32. pages 1-14. DOI:
10.1080/0951192X.2019.1571238.
- De Pace, F., Manuri, F., and Sanna, A. (2018) Augmented Reality
in Industry 4.0. Am J Compt Sci Inform Technol, 6:1, DOI:
10.21767/2349-3917.100017
- Faccio, M., Persona, A., Sgarbossa, F., and Zanin, G. (2014).
Industrial maintenance policy development: A quantitative framework.
International Journal of Production Economics, 147:85–93.
- Harrison, G. and Harrison, M. (2021). MongoDB Architecture and
Concepts, pages 13–32. Apress, Berkeley, CA.
- Havard, V., Baudry, D., Savatier, X., Jeanne, B., Louis, A., and
Mazari, B. (2016). Augmented industrial maintenance (aim): A case
study for evaluating and comparing with paper and video media
supports.
- In Augmented Reality, Virtual Reality, and Computer Graphics,
pages 302–320, Cham. Springer International Publishing.
- Jawarneh, I. M. A., Bellavista, P., Casimiro, F., Corradi, A.,
and Foschini, L. (2018). Cost-effective strategies for provisioning
nosql storage services in support for industry 4.0. In 2018 IEEE
Symposium on Computers and Communications (ISCC), pages 01227–01232.
- Hayder, Z., He, X., and Salzmann, M. (2017). Boundary-aware
instance segmentation. In Proceedings of the IEEE Conference on
Computer Vision and Pattern Recognition (CVPR).
- Karaagac, A., Haxhibeqiri, J., Ridolfi, M., Joseph, W., Moerman,
I., and Hoebeke, J. (2017). Evaluation of accurate indoor
localization systems in industrial environments. In 2017 22nd IEEE
International Conference on Emerging Technologies and Factory
Automation (ETFA), pages 1–8.
- Kontogiannis, S. and Asiminidis, C. (2021). Proposed management
system and response estimation algorithm for motorway incidents.
Energies, 14(10).
- Kychkin, A., Deryabin, A., Vikentyeva, O., and Shestakova, L.
(2019). Architecture of compressor equipment monitoring and control
cyber-physical system based on influxdata platform. In 2019
International Conference on Industrial Engineering, Applications and
Manufacturing (ICIEAM), pages 1–5.
- Lampropoulos, G., Siakas, K. and Anastasiadis, T. (2019).
Internet of Things in the Context of Industry 4.0: An Overview.
International Journal of Entrepreneurial Knowledge. 7. pages 4-19.
DOI: 10.2478/ijek-2019-0001.
- Liagkou, V., Salmas, D., and Stylios, Ch. (2019).
Realizing Virtual Reality Learning Environment for Industry 4.0, In
2019 12th CIRP Conference on Intelligent Computation in
Manufacturing Engineering, 79, ISSN 2212-8271.
- Nurelmadina, N., Hasan, MK., Memon, I., Saeed, RA., Zainol,
Ariffin KA., Ali, ES., Mokhtar, RA., Islam, S., Hossain, E., and
Hassan, MA. (2021). A Systematic Review on Cognitive Radio in Low
Power Wide Area Network for Industrial IoT Applications.
Sustainability. 13(1), pages: 338-358. DOI
https://doi.org/10.3390/su13010338.
- Pierdicca, R., Frontoni, E., Pollini, R., Trani, M., and
Verdini, L. (2017). The Use of Augmented Reality Glasses for the
Application in Industry 4.0. In 2017 International Conference on
Augmented Reality, Virtual Reality and Computer Graphics, pages.
389-401. DOI: 10.1007/978-3-319-60922-5_30.
- Profanter, S., Tekat, A., Dorofeev, K., Rickert, M., and Knoll,
A. (2019). OPC UA versus ROS, DDS, and MQTT: Performance evaluation
of Industry 4.0 protocols. In 2019 IEEE International Conference on
Industrial Technology (ICIT), pages 955–962.
- Saha, M., Nayak, S., Mohanty, N., Baral, V., and Rout, I.
(2021). Preterm delivery prediction using gradient boosting
algorithms. In Sharma, H., Gupta, M. K., Tomar, G. S., and Lipo, W.,
editors, Communication and Intelligent Systems, pages 59–68,
Singapore. Springer Singapore.
- Sanchez, M., Exposito, E., and Jose Aguila (2020). Industry 4.0:
Survey from a system integration perspective. International Journal
of Computer Integrated Manufacturing, 33:10, pp. 1017-1041
- Schmidt, J. F., Neuhold, D., Klaue, J., Schupke, D., and
Bettstetter, C. (2018). Experimental study of UWB connectivity in
industrial environments. In European Wireless 2018; 24th European
Wireless Conference, pages 1–4.
- Schuetz, M. (2016). Potree: Rendering large point clouds in web
browsers. Master's thesis, Institute of Computer Graphics and
Algorithms, Vienna University of Technology, Favoritenstrasse
9-11/E193-02, A-1040 Vienna, Austria.
- Silvestri, L., Forcina, A., Introna, V., Santolamazza, A., and
Cesarotti, V.(2020). Maintenance transformation through Industry 4.0
technologies: A systematic literature review, Computers in Industry,
123, ISSN 0166-3615.
- Tedjopurnomo, D. A., Bao, Z., Zheng, B., Choudhury, F., and Qin,
A. K. (2020). A survey on modern deep neural network for traffic
prediction: Trends, methods and challenges. IEEE Transactions on
Knowledge and Data Engineering, pages 1–1.
- TU Wien, I. (2016). Potree, a free open-source webgl based point
cloud renderer for large point clouds. https://potree.github.io/.
Accessed at: 15/7/2018.
- Wang, T., Leung, H., Zhao, J., and Wang, W. (2020). Multiseries
featural lstm for partial periodic time-series prediction: A case
study for steel industry. IEEE Transactions on Instrumentation and
Measurement, 69(9):5994–6003.
- Windeatt, T. (2008). Ensemble MLP Classifier Design, pages
133–147. Springer Berlin Heidelberg, Berlin, Heidelberg
- Wang, W., Yu, R., Huang, Q., and Neumann, U. (2018). Sgpn:
Similarity group proposal network for 3d point cloud instance
segmentation. In Proceedings of the IEEE Conference on Computer
Vision and Pattern Recognition (CVPR).
- Yassein, M. B., Shatnawi, M. Q., Aljwarneh, S., and Al-Hatmi, R.
(2017). Internet of things: Survey and open issues of MQTT protocol.
In 2017 International Conference on Engineering MIS (ICEMIS), pages
1–6.
- Zheng, Z., Wang, P., Ren, D., Liu, W., Ye, R., Hu, Q., and Zuo,
W. (2021). Enhancing geometric factors in model learning and
inference for object detection and instance segmentation. IEEE
Transactions on Cybernetics, pages 1–13.
BIOGRAPHICAL NOTES
Ion-Anastasios Karolos, holds a diploma in Rural and
Surveying Engineering (2012) and a Postgraduate Degree of Specialization
in Geoinformatics (2015). From January 2016 until the present, is a
Ph.D. Candidate in School of Rural and Surveying Engineering, Aristotle
University of Thessaloniki. His research interest mainly focuses on
hardware and software development of high precision GNSS receivers using
technologies like PCB designing (embedded design), 3D printing, and
smartphone applications. He is a member of the research project titled
"Liver3D" (https://www.liver3d.com/) for 3D printing of human liver for
medical purposes, co-funded by E.U. and National Funds. He has a lot of
programming experience using various programming languages (Swift,
Objective-C, Kotlin, Java, Python, C/C++) and software development kits
(iOS SDK, Android SDK).
Stylianos Bitharis, holds an MSc degree in
Geoinformatics with a specialization in Modern Geodetic applications and
his Ph.D. at the Department of Geodesy and Surveying (Faculty of
Engineering, School of Rural and Surveying Engineering) at the Aristotle
University of Thessaloniki. His Ph.D. research is related to GNSS data
analysis, Geodetic velocity estimation, and their implementation in
Geodetic Reference Frames.
Vasileios Tsioukas, Professor in the Dept. of
Geodesy and Surveying, School of Rural and Surveying Engineering,
Aristotle University of Thessaloniki. Education: Ph.D. in digital
Photogrammetry and Remote Sensing for the extraction of reliable
geometric information from close-range, aerial, and satellite sensors
(2000), B.Sc. in Electrical Engineering at the Aristotle University of
Thessaloniki. He has served as an assistant professor in the Dept. of
Architectural Engineering of the Democritus University of Thrace
(2003-2011). Visiting Professor (2005-2021) in the Postgraduate
Programme "Geoinformation in Environmental Management" at the
Mediterranean Agronomic Institute of Chania. Scientific co-operator of
the Cultural and Educational Technology Institute of Greece (CETI),
since 2004. His research has focused on Terrestrial Laser Scanning,
Mobil Mapping Systems, Photogrammetry and Remote Sensing for the
determination of 3D models of Cultural heritage, Digital Terrain Models
using stereoscopic aerial images and satellite SAR scenes for the
generation of orthoimages and large (1:50) and small scale maps
(1:50.000).
Christos Pikridas, Professor in the Dept. of Geodesy
and Surveying, School of Rural and Surveying Engineering, Aristotle
University of Thessaloniki. PhD in Satellite Geodesy by the same
University. He is currently the Director of the Geodetic methods and
Satellite Applications Lab. at the Department of Geodesy and Surveying
of AUTh. He is an expert on GNSS data analysis. He has over 20 years of
research experience on GNSS modeling error sources, algorithm
development, quality check and specifications for permanent GNSS
monitoring networks installation, GNSS applications in engineering
projects, and natural disaster monitoring and management.
Sotirios Kontogiannis, graduated from the Democritus
University of Thrace, Department of Electrical and Computer Engineering.
He received a M.Sc. in Software Engineering and Ph.D. from the same
department in the research area of algorithms and network protocols for
Distributed systems. He is currently a scientific staff member and
Director of the Distributed ΜicroComputer Systems Laboratory team MCSL
at the Dept. of Mathematics, University of Ioannina
Theodosios Gkamas, received his B.Sc. and M.Sc.
degrees in Computer Science from the University of Ioannina, Greece, in
2008 and 2010, respectively, while he obtained a Ph.D. degree in Signal
and Image Processing from the University of Strasbourg, France, in 2015.
He was a postdoctoral Researcher with CERTH-ITI in Thessaloniki during
2018-2019. In 2020, he started working as a Senior A.I. Researcher, Lead
A.I. Software Engineer, and Project Manager at the Department of
Mathematics in the University of Ioannina, Greece. His research
interests mainly include Signal and Image Processing, Medical Image
Analysis, Bioinformatics, Machine Learning, Deep Learning, Computer
Vision, Pattern Recognition and their application to Medical/Biological
Imaging, Industrial IoT sensory data, and financial data.
Nikolaos Zinas, holds a B.Sc. in surveying and
Mapping sciences, Msc. in Geodetic survey and Space Geodesy from
University of Nottingham and Ph.D. in Geomatic Engineering from
UCL. He is the Managing Director at TEKMON P.C., a software company,
building a digital workspace for the daily operations and critical
communications of the desk-less workforce. He has over 10 years of
experience, including general management and software product
development from idea to commercialization.
CONTACTS
Karolos, Ion Anastasios,
School of Rural and Survey-ing Eng.,
The Aristotle University of Thessaloniki,
Greece
Stylianos Bitharis,
School of Rural and Survey-ing Eng.,
The Aristotle University of Thessaloniki,
Greece
Vasileios Tioukas,
School of Rural and Survey-ing Eng.,
The Aristotle University of Thessaloniki,
Greece
Christos Pikridas,
School of Rural and Survey-ing Eng.,
The Aristotle University of Thessaloniki,
Greece
Sotirios Kontogiannis,
Dept. of Mathematics, University of Ioannina
MicroComputer Systems Laboratory team
Ioannina
GREECE
Theodosios Gkamas,
Laboratory of Distributed MicroComputer Systems MCSL,
Dept. of Mathematics,
The University of Ioannina,
Greece
Nikolaos Zinas,
Tekmon IKE,
Ioannina,
Greece